Stamping, a critical process in metal forming, involves various techniques to convert flat metal sheets into specific shapes through the use of dies and presses. The quality inspection of these stamped products is crucial for ensuring the final product meets the required standards and specifications. However, misconceptions in the inspection process can lead to inefficiencies, increased costs, and compromised product quality. This article aims to address these misconceptions and highlight the importance of accurate quality inspection in the stamping industry.
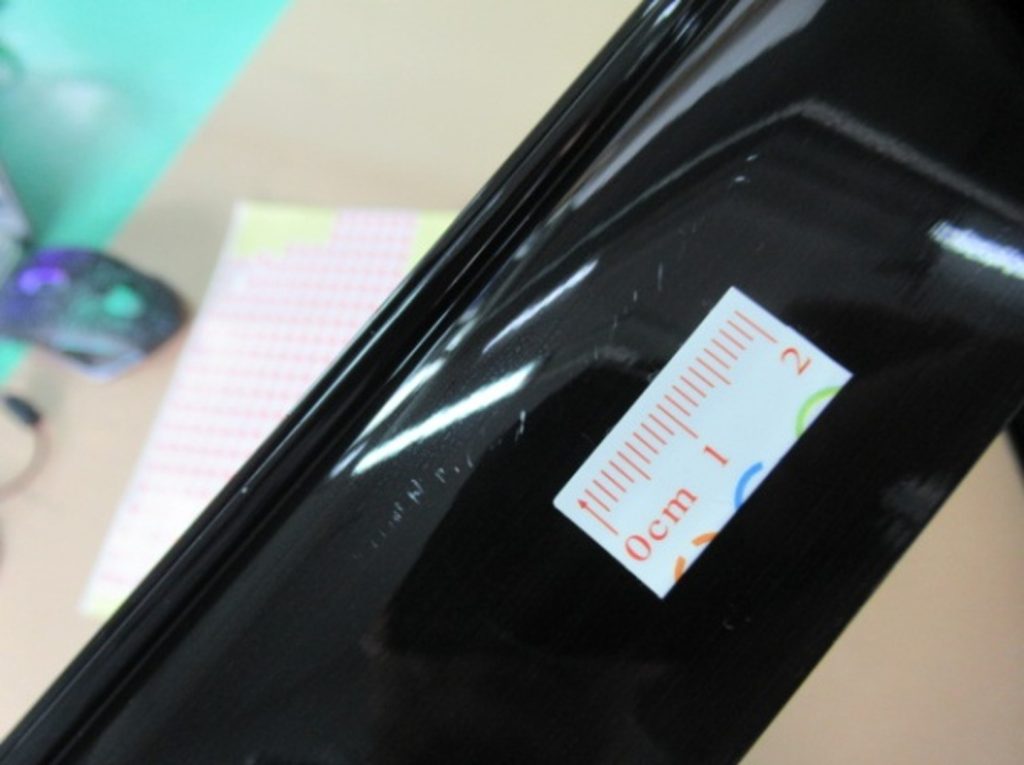
Contents
1. Misconception: Visual Inspection is Sufficient
One of the most common misconceptions in the inspection process of stamped products is the over-reliance on visual inspection. While visual inspection plays a vital role in identifying surface defects such as scratches, dents, and finishing inconsistencies, it falls short in detecting internal defects or dimensional inaccuracies that are not visible to the naked eye.
Solutions:
Integration of Non-Destructive Testing (NDT) Methods: Techniques such as ultrasonic testing, radiography, and magnetic particle inspection can identify subsurface and internal defects without damaging the products.
Adoption of Precision Measuring Tools: Tools like coordinate measuring machines (CMM), laser scanners, and micrometers can accurately measure the dimensions and geometries of stamped products, ensuring they meet the specified tolerances.
2. Misconception: 100% Inspection Guarantees Quality
Another misconception is the belief that inspecting every single item guarantees product quality. While 100% inspection may seem like a foolproof method to ensure quality, it is often impractical, costly, and time-consuming. Moreover, it does not guarantee the detection of all defects due to human error and the limitations of inspection methods.
Solutions:
Implementation of Statistical Quality Control (SQC): SQC techniques, such as sampling inspection and control charts, can effectively monitor and control the quality of stamped products without the need for inspecting every item.
Focus on Process Control: Improving the stamping process through regular maintenance of equipment, proper training of operators, and optimization of operating conditions can lead to a significant reduction in the occurrence of defects.
3. Misconception: All Defects are Equally Critical
Treating all defects with the same level of seriousness is a common oversight in the quality inspection process. Not all defects affect the functionality or aesthetic appeal of the stamped product to the same extent. Overemphasis on minor defects can divert resources from addressing more critical issues.
Solutions:
Adoption of a Risk-Based Approach: Classifying defects based on their impact on product performance and customer satisfaction allows for prioritizing the inspection and correction efforts towards critical defects.
Implementation of a Defect Severity Matrix: A matrix that categorizes defects by their severity and occurrence probability can help in making informed decisions on which defects to focus on during the inspection process.
4. Misconception: Manual Inspection is Obsolete
With the advancement of technology and the introduction of automated inspection systems, there is a misconception that manual inspection is obsolete. While automated systems offer speed and repeatability, they may not always be effective in detecting complex or nuanced defects that require human judgment.
Solutions:
Combining Manual and Automated Inspection: A hybrid approach that utilizes the strengths of both manual inspection for complex judgments and automated systems for repetitive tasks can provide a more comprehensive inspection strategy.
Continuous Training of Inspection Personnel: Ensuring that inspection personnel are well-trained in the latest inspection techniques and technologies can enhance the effectiveness of manual inspection.
5. Misconception: Inspection is the Sole Responsibility of Quality Inspectors
Finally, a significant misconception is that the responsibility for quality inspection lies solely with the quality inspectors. Quality assurance is a collective responsibility that involves every individual associated with the manufacturing process.
Solutions:
Promoting a Culture of Quality: Encouraging a quality-focused mindset among all employees, from the shop floor workers to the top management, ensures that quality is built into the product from the very beginning of the manufacturing process.
Involvement of Cross-Functional Teams: Engaging teams from different departments, including design, production, and engineering, in the quality inspection process can provide diverse perspectives and insights, leading to a more effective identification and resolution of quality issues.
In conclusion, addressing these misconceptions requires a comprehensive understanding of the stamping process, a commitment to quality at all levels of the organization, and the adoption of advanced inspection techniques and technologies. By moving beyond these misconceptions, manufacturers can significantly improve the efficiency and effectiveness of their quality inspection processes, resulting in higher-quality stamped products that meet or exceed customer expectations.