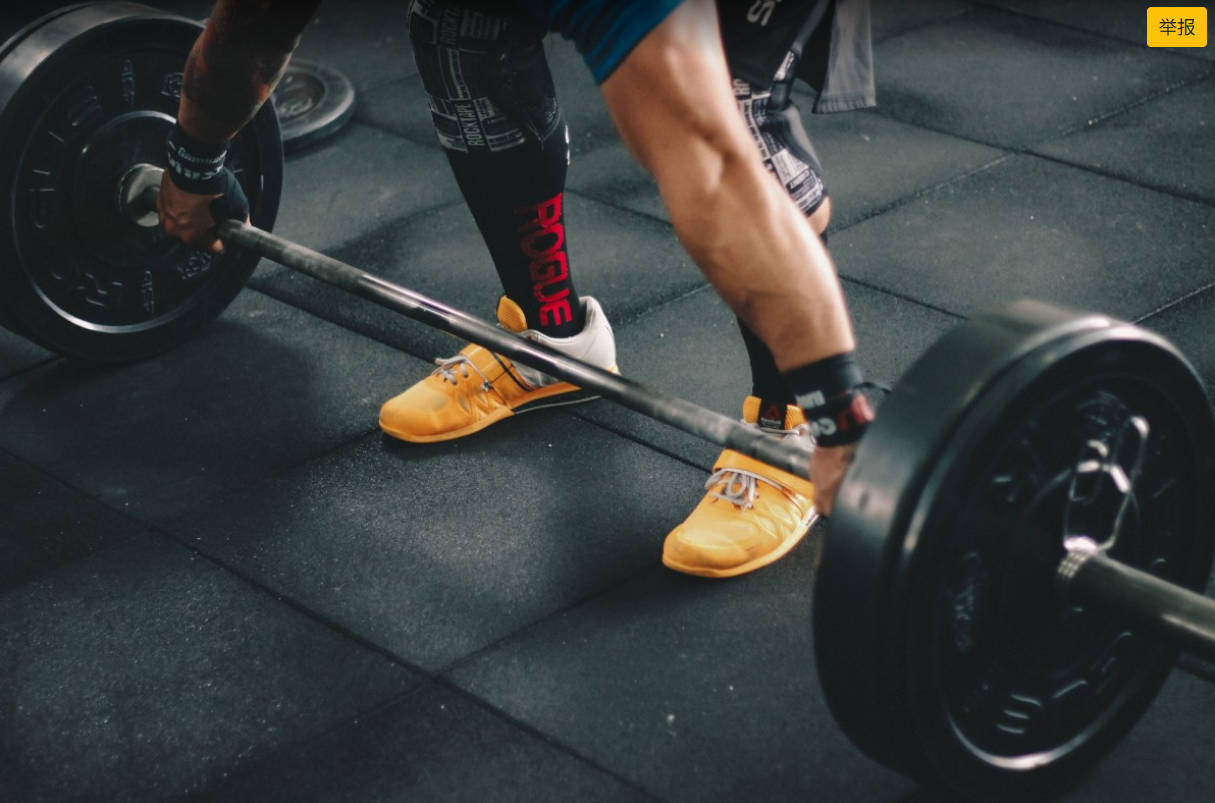
In the fast-paced world of the apparel industry, maintaining the highest standards of quality is not just a goal; it’s a necessity for customer satisfaction and brand integrity. Encountering a garment order rejection based on a third-party inspection report demands swift and decisive actions. This guide is designed to help clients navigate through the aftermath of such rejections, offering strategic insights into rectifying issues and ensuring the delivery of superior quality garments.
Introduction:
The apparel sector thrives on the bedrock of quality. In this fiercely competitive arena, third-party inspections serve as a critical checkpoint for assuring garment quality prior to shipment. A rejection in these inspections is a call to action for brands to address and rectify the underlying issues promptly, ensuring that only products meeting the highest standards reach their customers. This article delves into actionable strategies clients can employ to overturn inspection rejections, guaranteeing the excellence of their apparel products.
Strategic Steps for Quality Assurance Post-Inspection Rejection:
1.In-depth Inspection Report Analysis:
The first step following a rejection is a meticulous review of the inspection report. Pinpoint the specific reasons for rejection, whether they be material flaws, craftsmanship errors, or deviations from standards and regulations. Understanding these root causes is pivotal in formulating an effective rectification plan.
2.Manufacturer Engagement:
Open and clear communication with the manufacturer is vital. Share and discuss the inspection findings, emphasizing the need for clarity on each point of concern. Through collaborative discussions, both parties can align on corrective measures to address and resolve the identified issues.
3.Corrective and Preventive Measures:
Develop a comprehensive action plan with the manufacturer, detailing corrective steps and strategies to prevent future occurrences. This may include adjustments in quality control protocols, worker training enhancements, or the sourcing of better-quality materials.
4.Re-inspection for Quality Validation:
Implementing corrective actions should be followed by a re-inspection to confirm their effectiveness. Employing either the original inspection agency or a new one to review the revised production batch ensures that the modifications meet the required quality standards.
5.Ongoing Quality Monitoring:
Establish a regime for continuous quality monitoring and evaluation. This involves regular production checks, spontaneous inspections, and the tracking of quality metrics to swiftly identify and address any new issues. Open communication with the manufacturing partner is essential for timely problem-solving.
6.Supplier Collaboration and Relationship Building:
Cultivating a strong, collaborative relationship with suppliers is key to ongoing quality assurance. Foster an environment of mutual trust and open dialogue, encouraging suppliers to proactively engage in quality improvement efforts.
7.Supplier Performance Reviews and Development:
Integrate supplier performance evaluations into the quality assurance strategy. Set explicit performance benchmarks and regularly review supplier compliance. Offer feedback and guidance to aid in their development, sharing insights on best practices and regulatory changes to promote continuous improvement.
Conclusion:
A rejection in a third-party inspection is not merely a setback but an opportunity for brands to refine their quality control mechanisms. By thoroughly analyzing inspection reports, collaborating with manufacturers, enacting corrective measures, and committing to ongoing quality monitoring, brands can assure the superior quality of their apparel. Strengthening supplier relationships and fostering their development are also crucial steps in building a robust quality assurance framework. These measures not only safeguard the brand’s reputation but also enhance customer satisfaction, paving the way for enduring success in the competitive landscape of the apparel industry.