Wooden furniture has long been a popular choice for its aesthetic appeal, durability, and natural charm. When conducting furniture quality inspections, it is essential to understand the classification of wooden furniture based on materials. This article explores the major categories of wooden furniture, their distinctive characteristics, and how to ensure material compliance during furniture quality inspections.
Contents
Classification of Wooden Furniture by Materials:
1.Solid Wood Furniture:
Solid wood furniture is crafted entirely from a single type of wood, such as oak, mahogany, or walnut. It exhibits exceptional durability and longevity due to the inherent strength and stability of solid wood. Each piece showcases the unique grain patterns and natural beauty of the chosen wood species. Solid wood furniture provides a sense of luxury and is highly sought after for its timeless appeal. During quality inspections, it is crucial to verify the authenticity of the wood species used and assess any signs of wood defects or inconsistencies.
2.Veneer Furniture:
Veneer furniture features a thin layer of high-quality wood, known as veneer, adhered to a core material, typically plywood or medium-density fiberboard (MDF). Veneers offer the look and feel of solid wood while utilizing fewer precious resources. This type of furniture provides a wide range of design options, as different veneers can be applied to achieve various appearances and patterns. During inspections, it is vital to check the veneer quality, ensuring it is properly applied, free from bubbles, cracks, or peeling. The core material’s integrity, such as the thickness and strength of the plywood or MDF, should also be evaluated.
3.Plywood Furniture:
Plywood furniture is constructed using thin layers or plies of wood veneers stacked and bonded together with adhesive. This layered construction enhances stability and prevents warping or splitting. Plywood offers excellent strength and resistance to moisture, making it suitable for various furniture applications. During inspections, the quality and thickness of the veneer layers, the strength of the bonding, and the overall flatness and structural integrity of the plywood should be carefully examined.
4.Engineered Wood Furniture:
Engineered wood, also known as composite wood, is created by combining wood fibers, particles, or strands with adhesives and compressing them into a solid structure. Common types of engineered wood include particleboard, medium-density fiberboard (MDF), and oriented strand board (OSB). Engineered wood offers cost-effective alternatives to solid wood and exhibits consistent strength and dimensional stability. During inspections, it is important to assess the density, uniformity, and bonding strength of the engineered wood material, as well as check for any signs of delamination or surface defects.
5.Bamboo Furniture:
Bamboo furniture has gained popularity due to its sustainability, renewability, and unique aesthetic appeal. Bamboo is a fast-growing grass that can be harvested and replenished quickly. It offers strength comparable to hardwood and showcases a distinctive natural grain pattern. During inspections, it is essential to verify the authenticity of bamboo and evaluate its density, color consistency, and finish quality. The furniture’s construction and joinery should also be assessed for stability and durability.
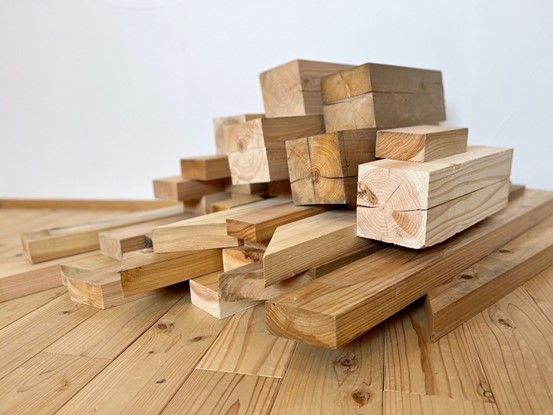
Ensuring Material Compliance in Furniture Quality Inspection:
To ensure that wooden furniture materials comply with standards during quality inspections, the following measures can be taken:
1.Standards and Regulations:
Familiarize yourself with local and international standards and regulations related to wooden furniture materials. This includes understanding permissible levels of formaldehyde emissions, chemical usage, and compliance with sustainability certifications such as Forest Stewardship Council (FSC) or Programme for the Endorsement of Forest Certification (PEFC).
2.Material Testing:
Perform material testing on wooden furniture components, such as wood species identification, moisture content analysis, adhesive strength tests, and formaldehyde emission tests. This ensures that the materials used meet the required quality and safety standards.
3.Supplier Evaluation:
Thoroughly assess the credibility and reputation of furniture suppliers. Conduct regular audits to ensure that they source materials from reputable and compliant sources. Maintain clear documentation and traceability of the materials used in each furniture piece.
4.Production Process Inspection:
Monitor the manufacturing process to ensure that materials are used correctly and in compliance with established standards. Regularly inspect the storage conditions of raw materials, adhesive usage, and adherence to proper techniques for cutting, shaping, and finishing wooden components.
5.Visual Inspection:
Perform visual inspections to identify any visible defects, inconsistencies, or non-compliant materials. This includes checking for proper wood grain matching, uniform finish application, absence of discoloration or stains, and adherence to design specifications.
Wooden furniture can be classified into various categories based on the materials used, each with its distinct characteristics and advantages. When conducting furniture quality inspections, it is crucial to ensure material compliance with relevant standards and regulations. By understanding the classification of wooden furniture materials, performing comprehensive inspections, conducting material testing, and evaluating suppliers, furniture manufacturers can ensure that their products meet the desired quality, safety, and sustainability requirements, satisfying customer expectations and enhancing the reputation of their brand.